EOS has released a new EOS M 290 1kW metal powder bed fusion (PBF) system, designed specifically with copper in mind. Initially developed by its custom machine building subsidiary, AMCM, the system is now available as a series model. The 3D printer measures 250x250x250 mm, has a 1kW laser, and can build at a rate of 27.8 mm³/h. The company is initially offering two qualified materials: CuCp, 99.95% pure copper for applications requiring electrical or heat conductivity, such as heat sinks, antennas, and wave guides; and EOS Copper CuCrZr, optimized for mechanical properties and heat treatment in addition to its conductive properties. This blend of chromium, copper, and zirconium is used for electrical connectors, heat exchangers, rocket combustion chambers, induction coils, and drive components.
With this new printer, EOS is catering to a booming market in the New Space and defense sectors for copper products. The company identifies energy, transport, and space as significant markets, with heat sinks and drives, heat management, and inductors highlighted as key components. Additionally, more industrial components are being manufactured in copper with additive manufacturing. In scenarios where brazing is required, such as in heating elements or induction coils, the high error rates in brazing can make 3D printing a viable alternative—as detailed in Additive Manufacturing Research’s “Copper Additive Manufacturing 2020–Market Database and Outlook” report on the topic. Optimized electrical drives can also be produced through 3D printing of copper. This could be useful for AM Ventures’ portfolio company Additive Drives.
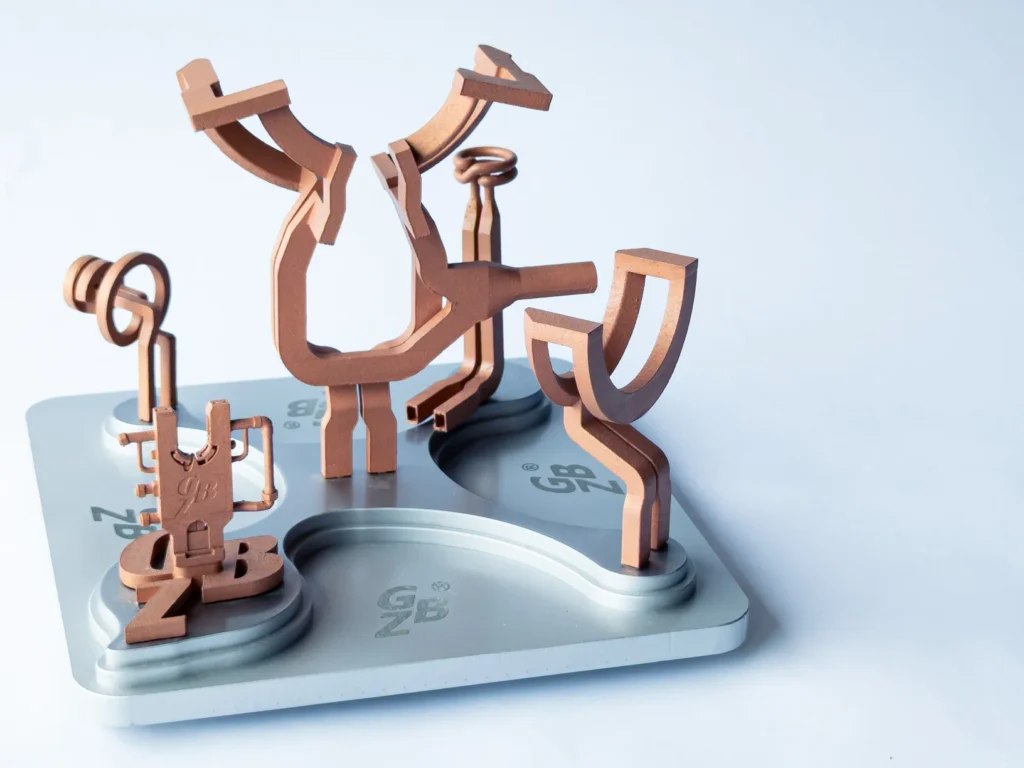
EOS is a bit late to the copper party, as Trumpf, for example, already offers the TruPrint 500 for copper, which uses a green laser operating at the 515 nm wavelength. Additionally, other copper materials are available on various platforms. However, the transition from AMCM to EOS is a brilliant approach. No matter how unconventional the required machine, AMCM can create it. This strategy provides bleeding-edge users in space and other sectors with an easy option to get a custom printer suited to their specific material or application. AMCM, being more client-focused and versatile than the larger EOS, can meet and cater to clients’ needs more swiftly.
This is, in and of itself, a great potential market for 3D printing. The additive manufacturing industry is transitioning from lab to fab, with more entities engaging in end-part manufacturing. Whereas an ideal prototyping machine would need to accommodate many materials and types of parts, in manufacturing, there is often a preference for an optimized machine tool designed to work with a single material. It’s common to print the same shape or the same family of shapes repeatedly. A machine tailored for one family of parts will be optimized for its purpose and the part family, making it significantly different from the more prototyping-oriented machines that are more commonplace today. Therefore, the approach of offering custom machines through AMCM and then serializing those that meet the needs of emerging customers is excellent. More companies should offer the same service. Some key applications, such as antennas or heat sinks, are likely to consume a disproportionate amount of machines in the coming years, highlighting this approach as a key differentiator for EOS.

“Our award-winning EOS M 290 is one of the most widely used metal AM machines in the world, and now the family is growing. Interestingly, the EOS M 290 1kW was developed by EOS’ AMCM group as part of its custom AM portfolio. The call to further commercialize this platform was exceptionally strong due to market demand, so now we are slip-streaming it into EOS’ broader portfolio,” said Monica Smith, EOS metal product line manager.
One company EOS references is inductor manufacturer GBZ Mannheim GmbH & Co.KG. Thomas Corell, Managing Director at GBZ Mannheim, stated:
“Additive manufacturing and the new one-kilowatt technology allow us to design and manufacture copper inductor applications that are more capable, durable and now produced in one piece with no soldering points. The core elements of inductor applications are now integrated in a single build, and the results are much higher optimization of the cooling channels, lower power consumption during the product lifecycle, and we are seeing great reproducibility on the production-side of things.”
Compared to brazing or other production methods, 3D printing can offer cost-effective production for components such as inductors, antennas, heat exchangers, and drive components. Less soldering equates to less manual labor, as well as a reduced chance of making expensive mistakes and generating less scrap. Further, design optimization could lead to higher performance than conventional methods. The excitement about inductors is well-founded, as antenna, heat exchangers, and drive components could also grow into significant applications. The M290 1 kW could turn out to be one of the most important machines of all.